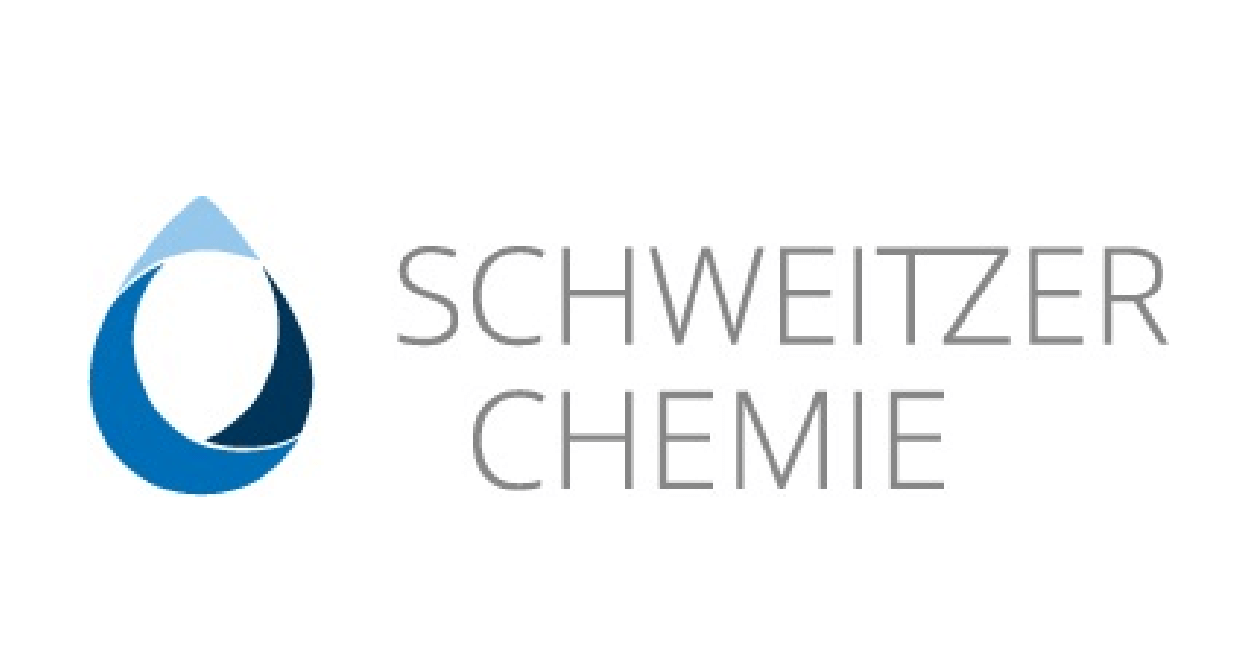
Healthy growth for Schweitzer Chemie
Thanks to YAVEON solution
Learn how Schweitzer Chemie replaced their self-programmed IT solution with a new ERP system and optimized their processes and find out how they established a basis for healthy growth.
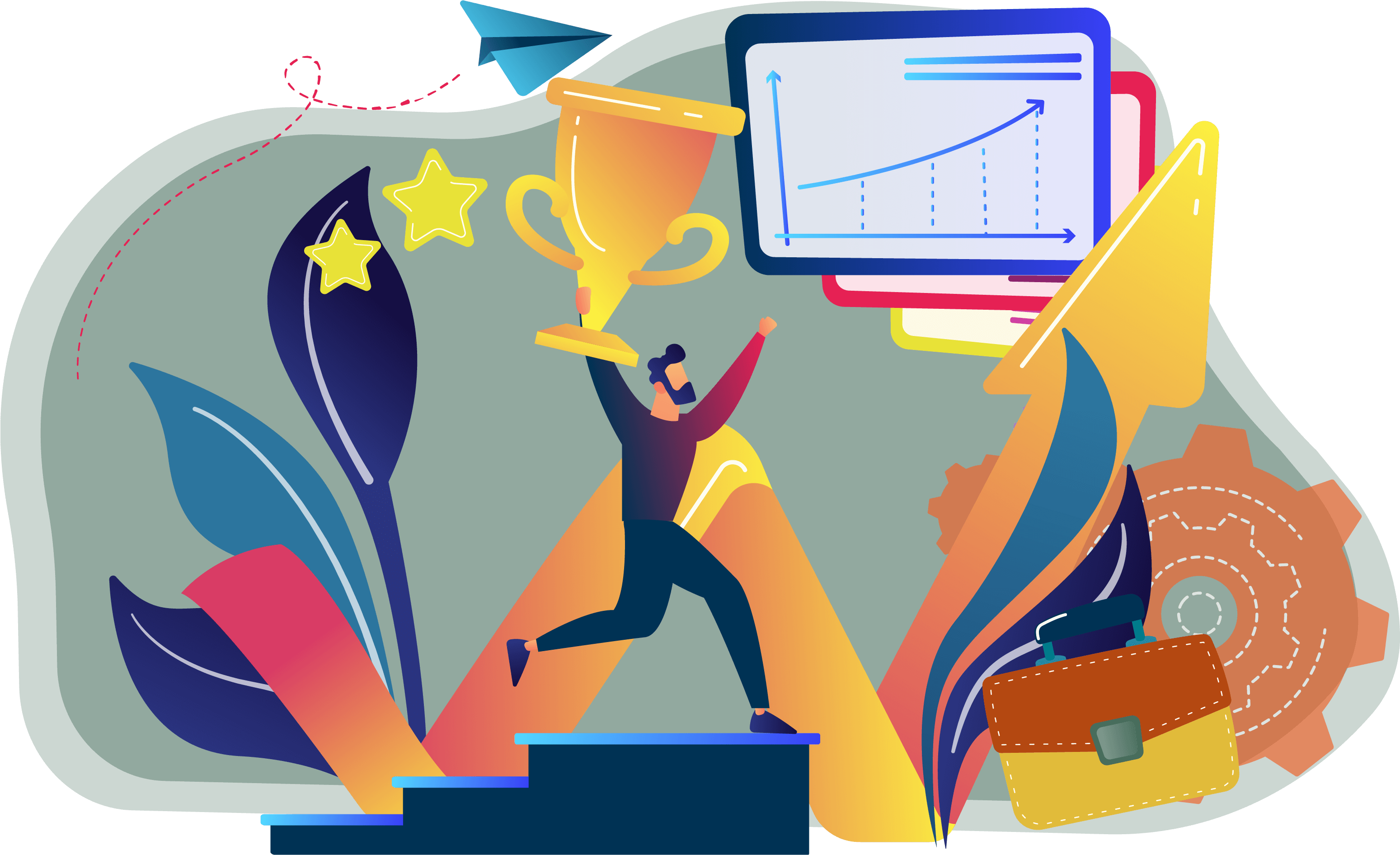
Everything at a glance
YAVEON ProBatch: New processes and structures
Customer
Schweitzer-Chemie GmbH | www.schweitzer-chemie.de
Focus
Chemical water treatment
Company Size
Approx. 180 Employees
Operating Model
On-Premises
Countries
Worldwide
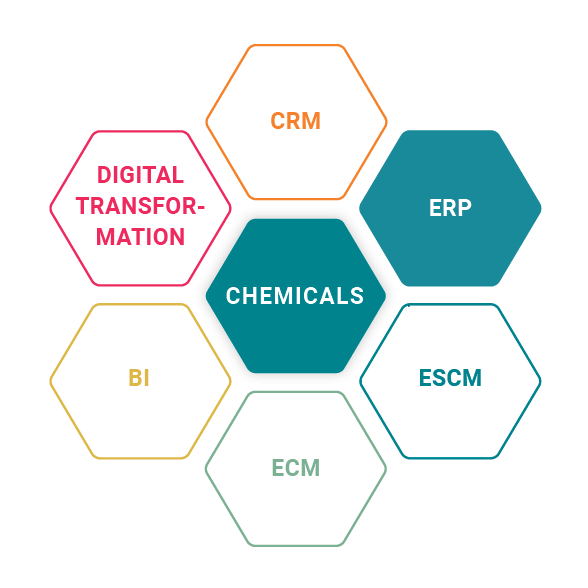
Want to read the reference report in one document?
Sure - simply download the PDF version of the report
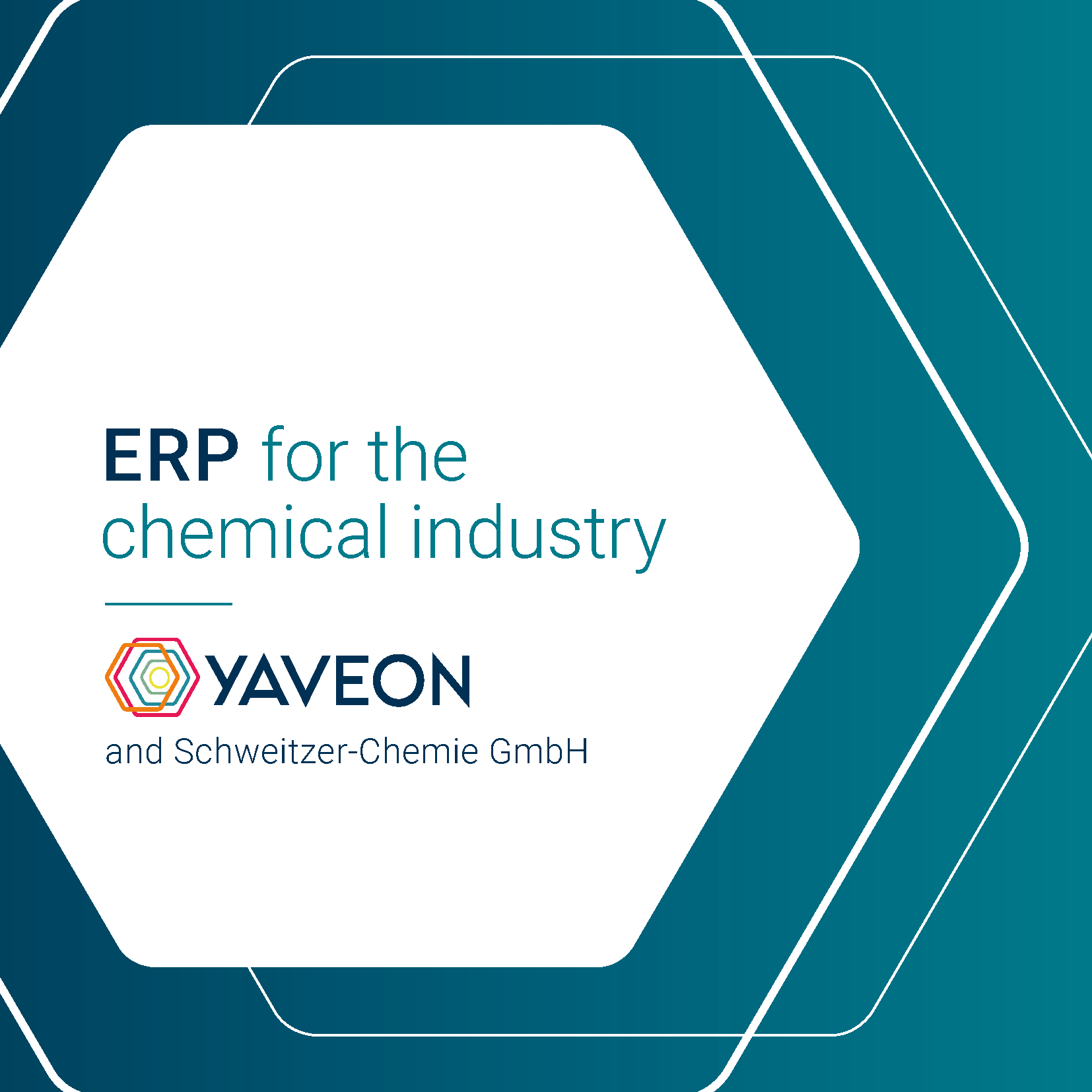
Which benefits does the YAVEON solution offer?
Visible results
CHALLENGES
- In-House programmed IT Solution
- Internal processes were no longer clear
- No growth due to undefined processes
SOLUTION
YAVEON introduced Microsoft Dynamics NAV as standard to enable completely new process modeling and define structures.
USE
- Competitive edge and a solid foundation for healthy growth
- ERP system is implemented according to specific requirements
- Interconnection of all three locations
Flourishing and successful
Schweitzer Chemie GmbH
What motivates a flourishing, successful company like Schweitzer Chemie GmbH to break away from current processes, rethink their entire IT process and separate themselves from established structures? What is it like to gradually eradicate an ERP system developed inhouse in order to switch to the modern Microsoft Dynamics NAV standard?
Wolfgang Eggerl, Managing Director of Schweitzer Chemie, sums it up quite simply: “Imagine that you want to build a house. If you want to build high, the foundation has to be right. Building this can sometimes be exhausting and you may need to knock down walls that are already built. But it’s worth it. Because if the foundation is stable, you can finally build sustainable walls.
Schweitzer Chemie GmbH works predominantly in the industrial sector, where water is used for versatile purposes: cooling, ventilation, drinking water. The company treats the water to destroy pathogens or to stabilize its hardness. As a final aspect, the Swabian company offers the largest service in the field of water treatment and treatment nationwide.
Behind these three pillars are around 180 employees, countless processes and an enormous array of technology. All this has to be recorded and optimized in a functioning ERP system. Thus far, the self-programmed IT solution “Kaktus“ supported this. When the decision was made to implement the NAV standard with YAVEON, it was clear that this project would be a mammoth task. A major point was the networking of all employees. Around one third work out of the office, so it is important to connect them safely and securely in order to strengthen communication. The leadership also wanted new, standardized procedures that YAVEON strongly supports in its development. “We finally had to think actively about processes,” explains Wolfgang Eggerl. The stated goal: to make Schweitzer Chemie fit for digitization and other innovations.
In the beginning there was the step backwards: “Until now, everything was programmed to suit our mouth, but the established structures and processes were simply incomprehensible and we were also not up to date with the latest technology. The master plan is here to use this standardization as a tool for complete process modeling. With a workforce of more than 180, this definition of processes is a fundamental factor for growth, speed and success.
The IT infrastructure must therefore be reengineered if it were to remain viable for the future. At the beginning, the change caused some problems. The leadership of Schweitzer Chemie were challenged to motivate the employees to adopt the new system. A completely new ERP system customized to meet the needs of the respective company, is not achieved overnight. They also faced some setbacks even after the implementation. Why would Schweitzer Chemie trust YAVEON to undertake such an elaborate project?
The overall goal is to cut costs, stay competitive and promote efficiency. At Schweitzer Chemie, networking between the three divisions plays an elementary role here. As a result, the same team should work more effectively, the costs per result should decrease and growth opportunities should be used. Using NAV, the processes are to be optimally optimized so that, instead of 30 orders, 50 orders can be carried out with the same team within the same period.
The master plan is to use standardization as a tool for complete process modeling.
Wolfgang Eggerl, Schweitzer-Chemie GmbH
The new software is becoming more and more familiar
Microsoft Dynamics NAV
The old structures and the old software are gradually disappearing and the new NAV software is becoming more and more familiar - because nobody from Schweitzer Chemie would want to go back to the old , In-House system. Wolfgang Eggerl describes the status quo as “wild time of change”. Even though the Swabian company still has to overcome hurdles in terms of the ERP system, especially in the service area, some processes have already improved considerably: in financial accounting, receipts and invoices can be processed more efficiently and logistics already works through Microsoft Dynamics NAV twice as fast.
The introduction of the ProMobile scanner solution also ensures the tracking of the batches of cleaning chemicals. Wolfgang Eggerl expects further significant improvement in the coming year. And above all through the interaction between software and people. Mr. Eggerl, hand on heart: Would you do it again? “There is always too little time for a project, there are always people who are against it. But the base we build on would never have changed, so we just started and I would do it again.“
Our status quo is a wild time of change.
Wolfgang Eggerl, Schweitzer-Chemie GmbH