7 measures to reduce your
storage costs
Reduce storage costs: We show you what role the process plays and how you can implement it successfully.
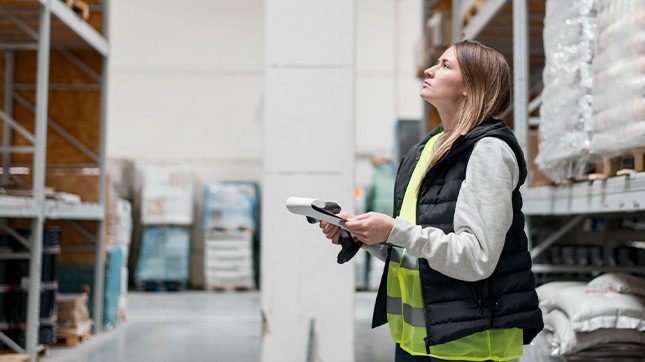
7. March 2024
As a manufacturing company, you spend a lot of time managing your own warehouse. Keeping an eye on stock levels, recording used materials and observing best-before dates: It's a lot of work, and your warehouse takes up a lot of space. All of this ties up liquidity - which you could put to better use elsewhere. The trick is to reduce your own storage costs and storage interest rates, resulting in increased liquidity. Our article reveals the importance of an efficient warehouse, what measures can be taken to reduce costs and how an ERP system can help.
What are storage costs, what are they and how are they made up?
Storage costs are all costs arising from the storage of goods. Examples of storage costs are
- Costs for the storage space such as rent, furnishings, energy, cleaning and maintenance
- Costs arising from stock such as spoiled goods or goods destroyed by improper storage
- Wage costs for employees who look after the warehouse
- Costs for materials in the warehouse such as packaging and office supplies
When calculating storage costs, a distinction is also made between two types: there are fixed and variable storage costs.
- Fixed storage costs are incurred on an ongoing basis, regardless of whether you are currently using your warehouse or not. These include, for example, rent, property tax and insurance
- Variable storage costs, on the other hand, are only incurred if your warehouse is actively used. These include costs for maintenance and cleaning, damaged goods and personnel costs.
What does it mean for companies to reduce storage costs?
Storage costs are a huge cost item for many companies. Is your warehouse large? That's when a lot of capital is tied up. This may sound unfavorable at first, but it has a huge advantage: it generates potential savings, as your expenditure can be sensibly reduced with a sensible warehouse. The newly generated liquidity can then be put to good use elsewhere. But be careful! A sure instinct is required when reducing storage costs. You should take a few challenges into account:
- If you reduce the amount of goods and materials in stock too much, this can lead to production bottlenecks, long waiting times or even production stoppages.
- Many warehouses are technologically completely outdated. Transparency, overview and good planning ability suffer as a result. If quantities and processes are also reduced, chaos quickly ensues.
- If responsibility for a warehouse lies solely in human hands, the dependency is high. If a single warehouse employee has all the information in their head and fails, companies are faced with a big question mark.
Now the question arises: What measures should you take to meet these challenges and reduce your storage costs at the same time?
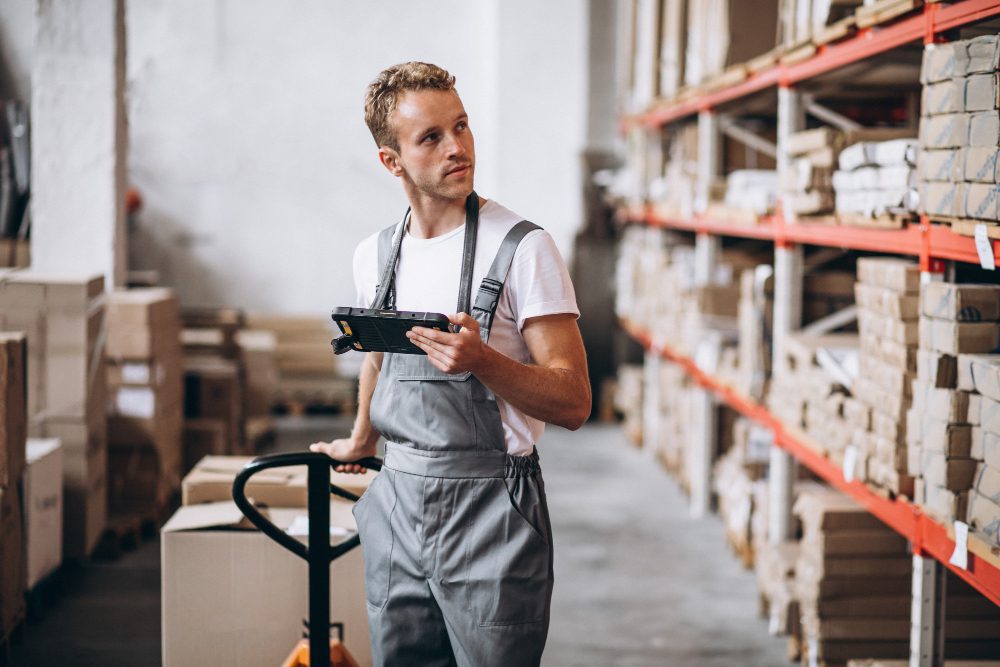
7 measures with which you can reduce your storage costs
On the way to lower storage costs, many companies rely on the following measures:
-
1. Make an inventory
Which goods are in stock? In what quantity are they available? Is the quality flawless or have defects occurred due to incorrect storage conditions, for example? Are there any slow-moving items that are not needed but are taking up capacity in the warehouse? During stocktaking, the entire stock on hand is examined in detail and documented. This allows you to calculate storage costs efficiently, resulting in storage interest. These include the costs of the capital tied up in stored goods. This creates transparency and the basis for rethinking and optimizing inventory. This is particularly useful for companies in industries that work with perishable goods, such as food and chemicals.
-
2. Reduce your capital commitment costs
Another measure to reduce financial expenditure in the warehouse is to reduce capital commitment costs. Based on the inventory carried out, you can reduce your stock of goods that are not profitable. This saves space and energy and eliminates the need for reordering. In addition, payment terms can be extended. If customers are given a shorter period and suppliers a longer period, the company's available liquidity increases. However, this step should be approached sensitively and coordinated with the partners concerned.
-
3. Minimize storage risks
Large warehouses harbor the risk of too many goods being in stock and, in the worst case, spoiling. This is a situation that companies in the food industry are particularly familiar with. By setting a storage period in advance and keeping an eye on it, you can minimize shrinkage.
-
4. Adapt your ordering and delivery processes
Rashly reordering goods without needing them unnecessarily increases storage costs. It is better if you receive goods on time and in the required quantity. Thanks to the just-in-time concept, you avoid overdeliveries and at the same time prevent bottlenecks - the best basis for an optimal ratio of your storage costs.
-
5. Set a minimum stock level
As a rule, your orders are within a rough range. However, unforeseen fluctuations can quickly become a problem if your stock is too low. You should therefore define a sensible minimum stock level with which you can react to an unexpected order situation.
-
6. Set a maximum stock level
But beware, the situation can also be exactly the opposite: Your orders reduce unexpectedly. It is important not to have too many perishable goods on site. Just like setting a minimum stock level, you should also think about a maximum stock level. What is the maximum quantity your warehouse can hold? Working out minimum and maximum quantities is a balancing act, but it's worth it.
-
7. Eliminate manual processes
Manual warehouse work is not only tedious, but also prone to errors. Stock can quickly be noted incorrectly, an order overlooked or an urgently needed colleague unavailable at short notice. Not to mention the time involved. To reduce your warehouse costs in the long term, you should say goodbye to manual processes and opt for a digital solution. The right software with the necessary functions provides an overview and less effort at the touch of a button. This also creates security, as fewer errors occur and you are able to react at any time. Enterprise Resource Planning (ERP) is the ideal basis for a sensible warehouse with reduced costs.
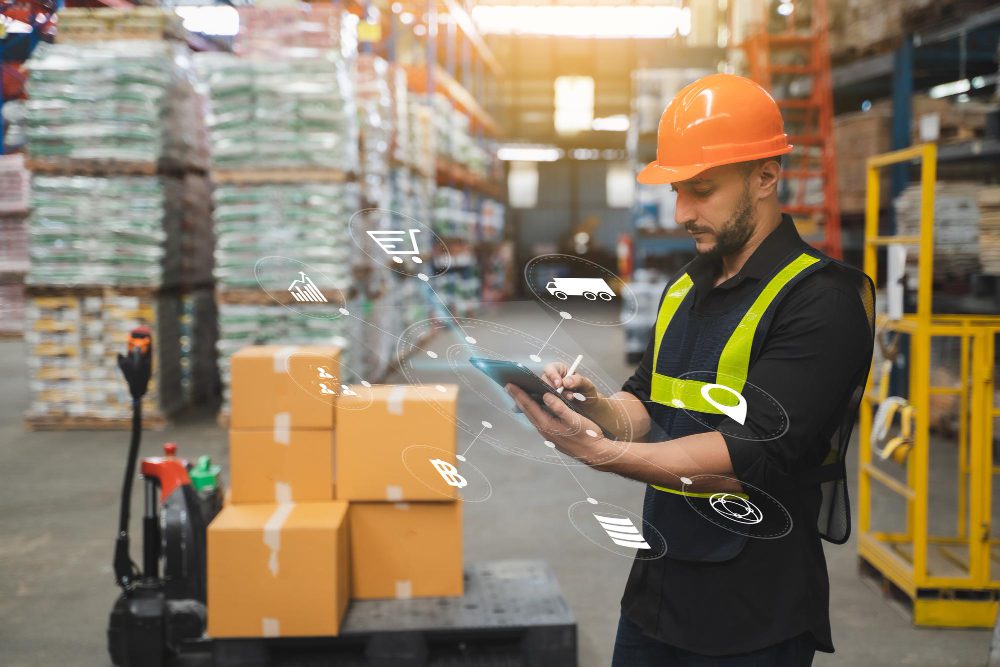
How does software help to reduce storage costs?
An ERP system creates the potential to digitize and automate all company processes - including warehouse processes. To reduce warehouse costs, ERP focuses on efficiency in the warehouse. If you manage to increase this, the workload is reduced automatically and costs fall. Typically, ERP systems help to reduce warehouse costs in the following ways:
- Goods and their movements in the warehouse are recorded using hand scanners. This increases the speed of the process and the timeliness of the information.
- An ERP is used to fully record and document not only the steps noted, but all steps in the entire warehouse process.
- Instead of having to process administrative tasks manually, your ERP handles inventory management by quantity and packages digitally.
- Because you can see an up-to-date list of all processes and stocks, stocktaking is easier.
- Similar to working with scanners in the warehouse, the automatic creation of labels and barcodes reduces your workload.
- You will be shown delivery and order suggestions directly.
- From quantity, best-before date or order requirement: the ERP shows you all the information in real time.
- Reports are not only easier to create digitally, but also faster and more accurate. This allows you to optimally align your processes with your company's overall strategy.
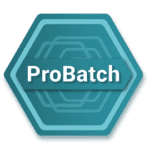
Microsoft Dynamics 365 Business Central is an ERP system that is ideal for start-ups, small and medium-sized companies. A good basis - from which much more can be gained. Our ERP industry solution YAVEON ProBatch is fully integrated into BC and enhances it with essential functions that turn a good standard system into a targeted specialist solution, for example for efficient warehouse management. This is made possible by our warehouse management module, ProBatch 365 Warehouse Management. These highlights await you with the solution:
- Management of load carriers directly in the system
- Search for storage space for storing items
- Incoming goods: load delivered goods onto load carriers and find a suitable storage location thanks to a set storage strategy
- Outgoing goods: control station with integrated traffic light functionality and picking planning
- By using replenishment orders, your picking area is constantly supplied with goods from other areas
- Picking sequence for stock reservation
- Possibilities around production provision
A wide range of options that simplify and optimally adapt your storage strategy. This makes it easier for you to find the balance between stock in the warehouse and reducing the storage quantity. The result: a secure, production-ready warehouse that frees up as much liquidity as possible.
How does an ERP system help companies in the life sciences to reduce storage costs?
Pharmaceuticals, biotechnology, chemicals, medical technology, food and cosmetics: for companies in the life sciences, there is great potential in an ERP system to reduce storage costs. Some of the main possibilities are
-
Pharmacy and biotechnology
An ERP system can help pharmaceutical and biotechnology companies reduce inventory costs by providing the following benefits:
- Avoidance of excess stock and stock shortages, which can lead to high storage and opportunity costs.
- Integration with other systems, such as quality management, batch tracking or sales, which ensures seamless traceability and a rapid response to customer requirements.
- Optimization of storage locations and routes, which increases the efficiency and utilization of the complex warehouse.
-
Chemistry
An ERP system supports the chemical industry in reducing storage costs by:
- This enables better planning and control of production processes, which optimizes stock levels and raw material requirements.
- It provides a transparent overview of all stock movements and stock levels, enabling effective stocktaking and fast delivery to customers.
- Ensures compliance with legal regulations and standards for the storage of chemicals, reducing the risk of penalties, accidents or environmental damage.
-
Food industry
An ERP system can help the food industry to reduce storage costs by:
- Traceability of all foods and their ingredients from procurement to distribution is guaranteed, enabling a rapid response to quality problems or recalls.
- Minimizing production downtime and waste is supported by precise demand planning and adjusting production volumes to customer orders.
- Promotes automation of business processes and a reduction in manual errors through seamless integration of all departments, suppliers and customers.
-
Cosmetics industry
To reduce storage costs for companies in the cosmetics industry, an ERP system offers these advantages, among others:
- A reduction in inventory costs through optimal inventory management that provides a real-time overview of stock levels, expiry dates and demand. An ERP system can also help to avoid overstocking by setting minimum stock levels, triggering automatic reorders and optimizing delivery times.
- Improve product quality and safety through full traceability of all raw materials, ingredients and finished products, ensuring regulatory compliance and effective quality control. An ERP system can also help reduce the risk of counterfeiting or contamination by verifying the authenticity of suppliers and the origin of products.
- An increase in customer satisfaction and loyalty through personalized and fast delivery tailored to individual customer needs and preferences. An ERP system can also help to increase customer loyalty by improving customer communication, feedback and service.
-
Medical technology sector
An ERP system can help the medical device industry reduce inventory costs by offering the following benefits:
- Optimization of warehouse processes and procedures through automation and integration of all warehouse data, which enables better planning, monitoring and control of inventory. An ERP system can also help to increase inventory turnover, reduce storage requirements and shorten delivery times.
Get to know our ERP industry solution
Use the potential of our ERP solution for optimum warehouse management and reduce your storage costs!