Kommissionierung
Was ist Kommissionierung?
Kommissionierung ist laut Definition die Zusammenstellung von Artikeln und Gütern für Aufträge für Kunden oder die Produktion. Die Person, die für die Zusammenstellung zuständig ist, wird als Kommissionierer, Greifer oder Picker bezeichnet.
Welche Rolle spielt die Kommissionierung in der Lagerlogistik?
Die Kommissionierung in der Logistik bezieht sich auf den Prozess des Zusammenstellens und Verpackens von Waren gemäß spezifischen Kundenaufträgen. Sie ist entscheidend für die Effizienz und Genauigkeit der Lieferkette, da sie sicherstellt, dass die richtigen Produkte in der richtigen Menge und Qualität an den Kunden versandt werden.
Eine gut organisierte Kommissionierung verbessert die Kundenzufriedenheit und reduziert Fehler sowie Zeit- und Kostenaufwände. Moderne Technologien wie Barcode-Scanner und automatisierte Systeme tragen zur Optimierung dieses Prozesses bei.
Sicherheit über das Lager hinaus: 5 Tipps, Rückrufe zu vermeiden.
Hat ein Produkt Ihr Lager verlassen, endet die Verantwortung? Falsch! Bei Qualitätsereignissen müssen Sie reagieren können. Mit unseren 5 Tipps vermeiden Sie Rückrufkationen und stellen Rückverfolgbarkeit sicher. Jetzt lesen!
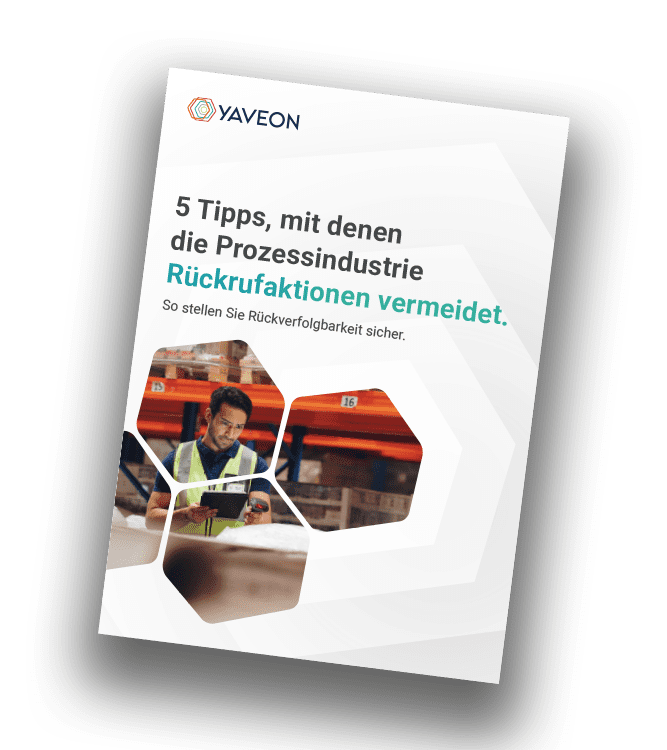
Wie ist der typische Ablauf der Kommissionierung in der Lagerlogistik?
Der Ablauf der Kommissionierung der Ware durchläuft folgende Prozessschritte:
-
1. Der Auftrag geht ein Zunächst wird ein Auftrag manuell oder automatisch erfasst. Alternativ erfolgt dies über ein E-Commerce-System.
-
2. Zusammenstellung des Auftrags Nun werden die Artikel ausgewählt, als Basis dafür dient der zugrundeliegende Auftrag.
-
3. Identifikation von Artikeln Mittels Barcodes, RFID-Tags oder Artikelnummern werden die benötigten Artikel identifiziert.
-
4. Artikelentnahme Im nächsten Schritt entnehmen die Kommissionierer die benötigten Artikel aus Regalen oder Behältern in der Lagerlogisitk. Typischerweise kommen hierzu Kommissioniertechniken wie die Staplerkommissionierung, Pick-by-Light oder das Voice-Picking zum Einsatz.
-
5. Mengenprüfung Sind die Artikel entnommen, wird die Menge mit dem Auftrag abgeglichen.
-
6. Verpacken Unter Einhaltung der Verpackungsvorschriften wird der Auftrag nun verpackt.
-
7. Qualitätskontrolle Bevor die kommissionierte Ware zum Versand geht, wird sie einer Qualitätskontrolle unterzogen.
-
8. Versand Im letzten Schritt wird die Lieferung verschickt oder alternativ im Lager hinterlegt, um später weiter bearbeitet werden zu können.
Welche Arten der Kommissionierung gibt es?
Manuelle Kommissionierung
Bei der manuellen Kommissionierung übernehmen geschulte Mitarbeiterinnen und Mitarbeiter den gesamten Kommissionierprozess.
Vorteile:
- Individuelles Reagieren auf einzelne Aufträge
- Teamarbeit möglich
Nachteile:
- Fehleranfällig
- Abhängigkeit von Anwesenheit der zuständigen Personen
Automatisierte Kommissionierung
Bei der automatischen Kommissionierung handhaben Picking-Roboter einzelne Kisten oder auch Lager.
Vorteile:
- Mehr Effizient und Effektivität bei der Lagerarbeit
- Laufende Kosten lassen sich reduzieren
Nachteile:
- Stillstand beim Ausfall der Roboter
- Meist relativ aufwendige Installation und Integration in Lager bzw. Systemlandschaft
Welche Kommissioniermethoden gibt es?
Einstufige Kommissionierung (Auftragsorientiert)
Bei der einstufigen Kommissionierung wird ein Auftrag direkt im Lager oder in der Produktion kommissioniert. Dafür geht der zuständige Mitarbeiter zum Lagerplatz, nimmt die Ware auf und legt sie in den dafür vorgesehenen Behälter.
Vorteile:
- Unkompliziertes Verfahren, für das kein spezielles Kommissioniersystem benötigt wird
- Lagerzonen werden einfach aufgeteilt
- Schnelle Kommissionierung einzelner Kundenaufträge
Nachteile:
- Kundenaufträge werden nicht optimal zusammengestellt
- Es kann zu langen Wegstrecken kommen
- Es ist keine serienorientierte Verarbeitung möglich
Auftragsorientierte serielle Kommissionierung
Die auftragsorientierte serielle Kommissionierung stellt die einfachste Kommissioniermethode dar. Hierbei wickelt der Kommissionierer alle Aufträge in zeitlicher Reihenfolge nacheinander ab. Lagerzonen können dabei durchschritten werden.
Vorteile:
- Einfache Einarbeitung
- Verantwortlichkeiten sind schnell festgelegt
- Wenig organisatorischer Aufwand
Nachteile:
- Lange Durchlaufzeiten der Aufträge
- Lange Kommissionierwege
- Aufwändige Auftragsübergabe an der Lagerzone an den nächsten zuständigen Kommissionierer
Auftragsorientierte parallele Kommissionierung
Auch bei der auftragsorientierten parallelen Kommissionierung besteht der Auftrag aus mehreren Positionen aus verschiedenen Zonen im Lager. Die Methode wird besonders bei aufgeteilten Aufträgen genutzt. Sind die Teilaufträge abgeschlossen, folgt eine Zusammenführung zum Gesamtauftrag.
Vorteile:
- Kommissionierzonen werden in kleine Bereiche aufgesplittet
- Damit kürzere Wege und Durchlaufzeiten
Nachteile:
- Die Teilaufträge müssen an einer Konsolidierungsstelle wieder vereint werden
Zweistufige Kommissionierung
Die zweistufige Kommissionierung wird auch serienorientierte parallele Kommissionierung genannt und kommt meist zum Einsatz, wenn mehrere Einzelpositionen eines Produktes bearbeitet werden sollen.
Vorteile:
- Lagerplatz muss vom Kommissionierer nur einmal angelaufen werden
Nachteile:
- Vorbereitung und Zusammenführung der Aufträge sehr aufwändig
Mehrstufige Kommissionierung
Bei der mehrstufigen Kommissionierung werden mehrere Kundenaufträge auf einmal parallel bearbeitet. Abhängig von Lagertyp und -zonen erfolgt erst die Kumulierung der Aufträge. Deren Verteilung zu den Aufträgen erfolgt im Anschluss an der Packstelle.
Vorteile:
- Kommissionierer kann zahlreiche Artikel aus einem Lagerfach zeitgleich entnehmen.
Nachteile:
- Große Stückzahlen müssen manuell gezählt werden, was aufwändig und fehleranfällig ist.
Batch-Kommissionierung
Batch-Kommissionierung wickelt Kommissionieraufträge anhand einem geplanten Prinzip ab. Die nötigen Artikel werden in einem „Batch“, also artikelreinen Chargen, zusammengefügt und im Anschluss bearbeitet.
Vorteile:
- Mehr Effizienz, da die Bearbeitung zusammengefasst erfolgt
- Weniger Laufwege
Nachteile:
- Zeitaufwand, da zunächst alle Aufträge in Chargen gesammelt werden
- Wenig Flexibilität, da unterschiedliche Aufträge jeweils einzeln angelegt werden müssen
Welche Prinzipien der Kommissionierung gibt es?
Statische Kommissionierung
Bei der statischen Kommissionierung bewegt sich die zuständige Person jeweils zum einzelnen Lagerplatz. Der Artikel wird hier vor Ort entnommen. Sie wird auch Mann-zu-Ware-Kommissionierung genannt.
Dynamische Kommissionierung
Bei der dynamischen Kommissionierung lagert das Lagerverwaltungssystem die Lagereinheit automatisch aus und bewegt sie zur Kommissionierstelle, wo die nötige Menge entnommen wird. Der Ladungsträger wird nun erneut automatisiert eingelagert. Ware-zum-Mann.
Welche Technologien und Hilfsmittel können bei der Kommissionierung eingesetzt werden?
Pick-by-Voice
Pick-by-Voice-Systeme verwenden sprachgesteuerte Anweisungen, die über Headsets an die Mitarbeiter weitergegeben werden, was freihändiges Arbeiten ermöglicht und Fehler reduziert.
Vorteile:
- Freihändiges Arbeiten: Mitarbeiter können beide Hände frei nutzen, was die Effizienz und Ergonomie verbessert.
- Flexibilität: Kann in verschiedenen Lagerumgebungen eingesetzt werden, auch in solchen, wo visuelle Hilfsmittel stören könnten.
Nachteile:
- Anfangsinvestition: Hohe Kosten für die Anschaffung und Implementierung der Systeme.
- Abhängigkeit von Sprache: Starke Akzente oder Sprachbarrieren können die Effektivität beeinträchtigen.
Pick-by-Light Systeme
Pick-by-Light-Systeme nutzen visuelle Signale, um den Mitarbeitern den richtigen Entnahmeort anzuzeigen, was eine schnelle und fehlerfreie Kommissionierung unterstützt. Beide Systeme erhöhen die Effizienz und Genauigkeit in der Lagerhaltung.
Vorteile:
- Visuelle Führung: Leuchtanzeigen an den Lagerplätzen ermöglichen eine schnelle und intuitive Entnahme, was die Kommissioniergeschwindigkeit erhöht.
- Hohe Genauigkeit: Die visuelle Unterstützung reduziert Fehler und erhöht die Genauigkeit der Entnahmen.
Nachteile:
- Kosten: Hohe Anschaffungskosten für die Installation der Leuchtsysteme und die Integration in das Lagerverwaltungssystem.
- Eingeschränkte Flexibilität: Weniger geeignet für dynamische Lagerumgebungen, in denen sich die Lagerplätze häufig ändern.
Automatisierte Lagersysteme (AS/RS)
Automatisierte Lagersysteme (AS/RS) verwenden computergesteuerte Maschinen zur automatischen Ein- und Auslagerung von Gütern, was eine optimale Raumausnutzung und hohe Effizienz ermöglicht. Diese Systeme sind ideal für Lager mit hohem Durchsatz und beschränktem Platz und verbessern die Bestandsgenauigkeit durch Echtzeit-Datenerfassung. Sie reduzieren manuelle Eingriffe und erhöhen die Sicherheit, indem sie Arbeitsunfälle minimieren.
Barcode- und RFID-Technologie
Barcodes und RFID-Technologien werden in der Kommissionierung zur schnellen und fehlerfreien Datenerfassung genutzt. Barcodes werden gescannt, um Informationen in einem Lagerverwaltungssystem zu speichern, während RFID-Tags drahtlos und ohne Sichtverbindung ausgelesen werden können. Beide Technologien verbessern die Bestandsgenauigkeit und reduzieren manuelle Eingabefehler, wodurch die Effizienz im Lagerbetrieb gesteigert wird.
Wie kommissioniert man richtig?
Die folgenden Tipps können die Kommissionierung der Ware in Unternehmen deutlich erleichtern:
- Gute Lagerorganisation und Lagerlogisitk für leichte Auffindbarkeit und Übersicht
- Einsatz eines geeigneten Kommissioniersystems
- Optimierung der Gehwege
- Kommissionierer ausführlich schulen
- Leistungskennzahlen wie die Geschwindigkeit und Fehlerquote im Auge behalten und bei Bedarf reagieren
- Zuverlässige Qualitätsmechanismen etablieren
- Technologien und Roboter einsetzen
- Bestehende Prozesse kontinuierlich verbessern
- Sichere Bedingungen zum Beispiel durch Sicherheitsausrüstung und einen geeigneten Arbeitsplatz
YAVEON ProBatch: Unterstützung der Kommissionierung in der Prozessindustrie
Mit der ERP-Software YAVEON ProBatch revolutionieren Sie Ihre Kommissionierungsprozesse – für eine fehlerfreie, effiziente und qualitativ hochwertige Abwicklung Ihrer Aufträge. Profitieren Sie von einer Lösung, die speziell auf die Anforderungen der Prozessindustrie zugeschnitten ist.
- Chargenrückverfolgbarkeit: Mit YAVEON ProBatch genießen Sie absolute Sicherheit durch vollständige Rückverfolgbarkeit Ihrer Chargen. Stellen Sie sicher, dass stets die richtigen Chargen kommissioniert werden, minimieren Sie Fehler und halten Sie höchste Qualitätsstandards ein.
- Mobiles Kommissionieren: Erleben Sie eine neue Dimension der Effizienz mit mobiler Kommissionierung. YAVEON ProBatch ermöglicht es Ihren Lagerarbeitern, Aufträge in Echtzeit zu erhalten und zu bearbeiten. Steigern Sie die Produktivität und verkürzen Sie die Bearbeitungszeiten drastisch.
- Qualitätskontrollen: Vertrauen Sie auf höchste Produktqualität mit integrierten Qualitätskontrollen. Nur freigegebene und geprüfte Chargen werden kommissioniert, was die Qualität Ihrer Produkte sichert und das Risiko von Rückrufaktionen minimiert.
- Steuerung der Kommissionierung durch Prioritäten: Optimieren Sie Ihre Lagerbestände durch intelligente Prioritätssteuerung. YAVEON ProBatch berücksichtigt das Zugangs- oder Ablaufdatum (FEFO) sowie den Gebindeanbruch, sodass Bestände mit niedrigerer Priorität zuerst verwendet werden. Dies garantiert eine effiziente Lagerverwaltung.
Weil es sich automatisiert einfacher kommissioniert.
Kommissionierung planen oder erstellen? Mit unserer ERP-Branchenlösung YAVEON ProBatch automatisieren Sie beides. Jetzt unverbindlich kennenlernen und mit Links kommissionieren!
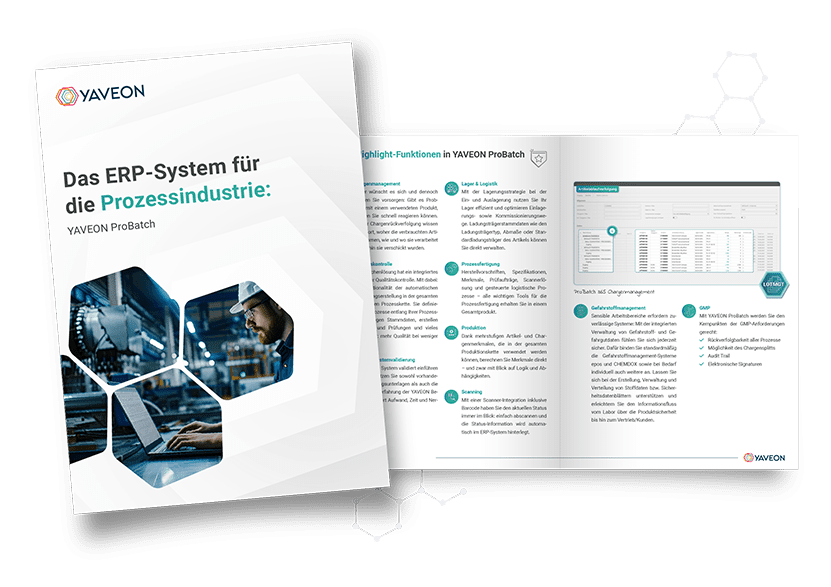
Beitrag teilen
Autor
Weitere interessante Beiträge